垃圾发电厂垃圾堆酵渗滤液处理技术--广州勃发
发布时间:2024-12-04 点击次数:305
在垃圾发电的复杂流程中,堆酵渗滤液的处理成为了至关重要的环节。垃圾发电厂通过燃烧垃圾产生热量来实现发电目的,而新鲜垃圾被运抵发电厂的储存池后,需经历一定天数的堆积发酵过程。这一过程旨在降低垃圾的含水率,从而提升垃圾焚烧发电的效率,而在此期间,从垃圾中渗滤出的废水被收集起来,便形成了我们所关注的发电厂堆酵渗滤液。
水量规模显著:其水量的大小与垃圾发电系统的规模以及产线数量紧密相连,通常每天的水量可达 100 立方米至数百立方米不等,如此规模的水量,对处理工艺的处理能力提出了严峻挑战。
高浓度污染物指标:COD(化学需氧量)和氨氮浓度令人瞩目,COD 浓度范围约在 30000 - 80000mg/L,氨氮浓度则在 1000 - 10000mg/L 之间。如此高浓度的污染物意味着处理过程中需要强大的降解能力和高效的处理手段,才能将其净化至符合要求的水平。
油脂含量颇高且多变:油脂含量可高达几千甚至上万毫克每升,并且这一数值与垃圾分类的精细程度以及地域生活习惯有着千丝万缕的联系。例如,在某些饮食文化较为油腻的地区,垃圾中的油脂含量可能会显著偏高,这进一步增加了渗滤液处理的复杂性。
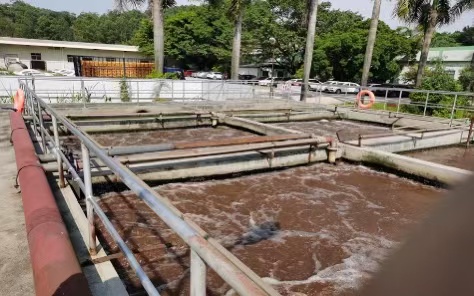
零排放愿景与回用路径:垃圾发电厂致力于实现废水处理后的零排放目标,具体的实现方式是将处理后的废水回用于发电厂冷却循环水补水。这不仅能够有效减少水资源的浪费,还能在一定程度上降低对外部水资源的依赖,提高发电厂的水资源利用效率和环境友好性。
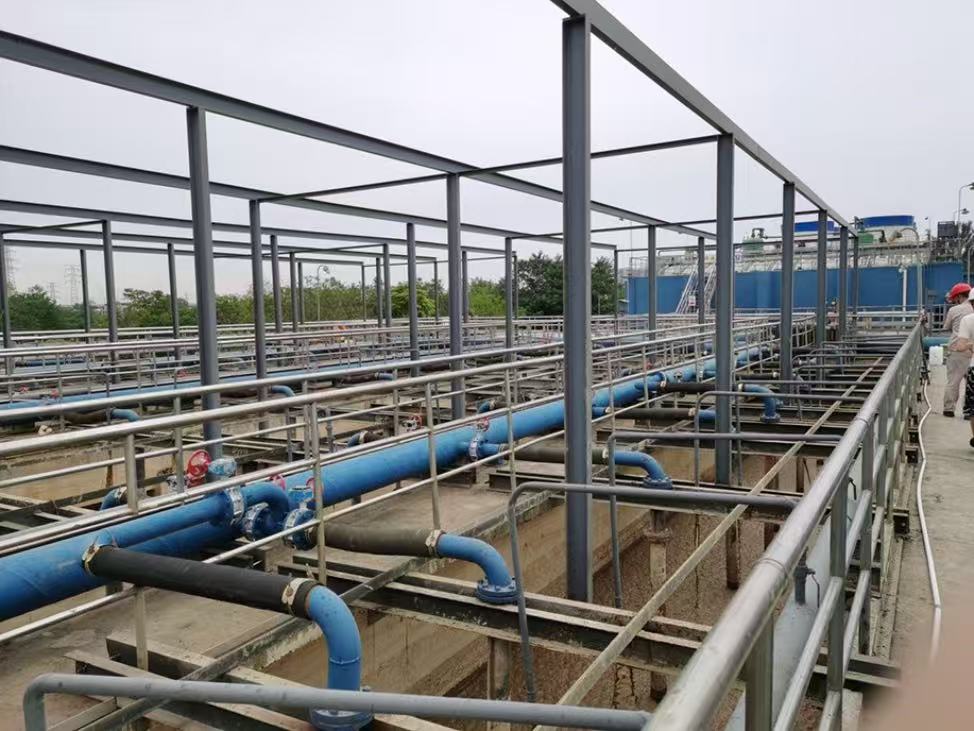
严苛的回用水质标准:处理后的出水需严格执行《城市污水再生利用工业用水水质》(GB/T 19923 - 2005)中关于敞开式循环冷却水水质的标准。这一标准对水中的各项指标,如硬度、酸碱度、悬浮物、重金属含量等都有着详细且严格的规定,要求处理工艺必须具备精准的调控能力和高效的净化能力,以确保回用水质的稳定性和安全性。
当前,众多垃圾发电厂普遍采用 “预处理 + 大型厌氧反应罐 + A2O/SBR + MBR + 双膜(UF + RO)” 工艺来处理堆酵渗滤液。尽管该系统的膜产水在一定程度上能够满足回用需求,但在实际运行过程中,却暴露出诸多棘手问题。
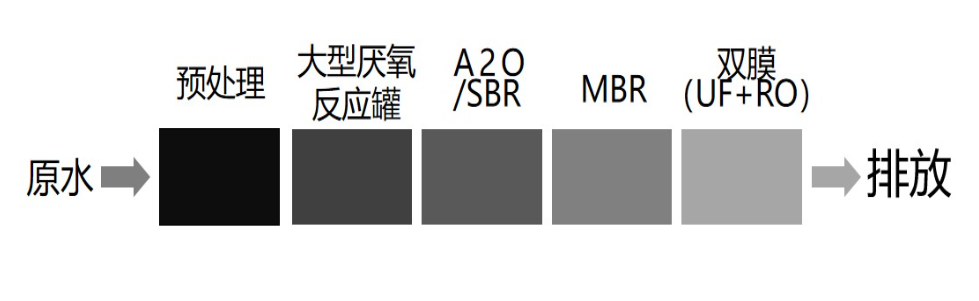
预处理短板与生化低效:预处理环节相对简单,未能对渗滤液进行充分的前期处理,导致后续生化效果大打折扣,效率低下。同时,这也使得整个处理系统的设备占地面积庞大,例如厌氧停留时间常常需要 15 天以上,甚至更长时间,这不仅增加了建设成本,还降低了处理效率,在空间利用和处理时效上都存在明显不足。
生化深度不足与残留污染:生化系统的出水处理深度不够,即使经过 MBR 处理后,出水的 COD 仍高达约 300 - 500mg/L。这表明生化过程未能充分降解污染物,残留的高浓度 COD 对后续膜处理系统造成了巨大压力,也难以满足严格的回用水质标准。
膜系统困境与回收率下滑:膜系统的回收率较低,初期浓液产率就达到约 20 - 30%。随着长时间运行,膜污堵现象愈发严重,如同血管堵塞一般,导致浓液产生率急剧下降,最终使得回用水回收率低于 60%。这不仅造成了大量水资源的浪费,还增加了浓液处理的难度和成本,成为整个处理工艺的瓶颈之一。
高昂投资与设备局限:设备投资成本居高不下,由于常规卷式耐污染膜难以承受渗滤液的恶劣工况,极易出现故障瘫痪,不得不采用造价更高的 DTRO(碟管式反渗透膜)。这使得系统总投资高达约 10 - 12 万元 / 吨水・天,高额的投资成本让许多发电厂望而却步,也限制了该工艺的进一步推广和优化。
浓液难题与负面效应:浓液中的有机物浓度极高,若直接将其用作脱硫脱硝石灰制浆,会带来一系列负面影响。例如,可能会影响石灰制浆的质量和效率,导致脱硫脱硝效果不佳,同时还可能引发设备腐蚀、堵塞等问题,增加设备维护成本和运行风险。
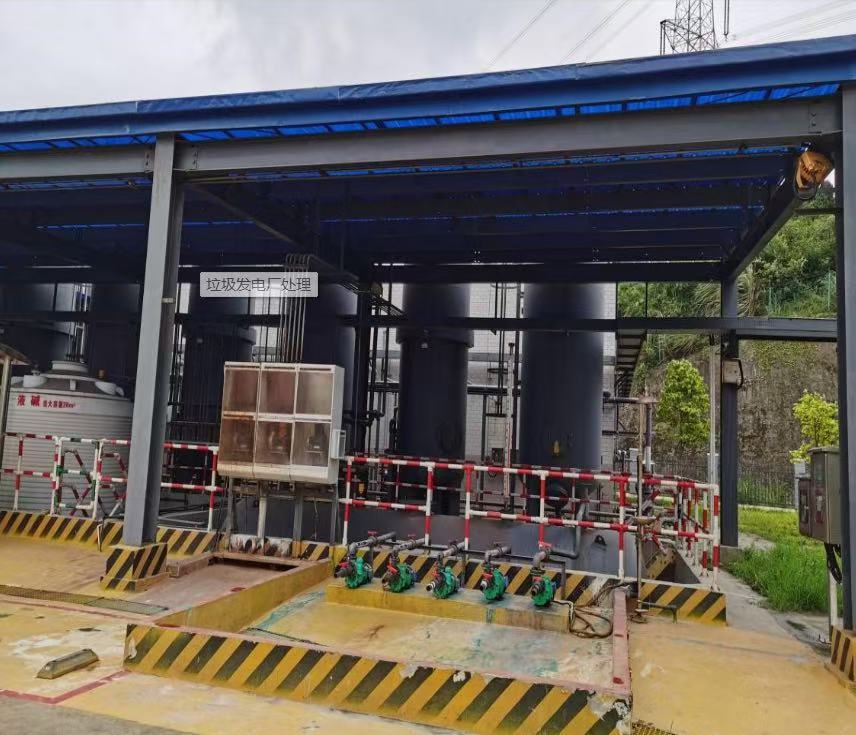
创新工艺路线与核心创新点:针对传统工艺的种种弊端,一种全新的 “原水 + 高效预处理 + 高效厌氧 + 生化 + 高级氧化深度处理 + 回用系统(UF + RO)” 组合创新工艺应运而生。其创新亮点主要体现在两个关键环节。首先,在厌氧生化前进行高效预处理,这一举措能够去除 30% 以上的 COD,同时有效去除浮油并消耗酸化产生的酸,从而大大减轻了后端厌氧及生化系统的负荷,为后续处理过程奠定了良好的基础。其次,采用高级氧化深度处理技术,将生化出水直接处理至达到排放标准(COD<100mg/L)。这一深度处理不仅能够确保出水水质符合严格的环保要求,还能显著减轻膜系统的污染程度和清洗强度,降低膜运行费用,延长膜的使用寿命,如同为膜系统穿上了一层 “防护衣”,使其能够更高效、稳定地运行。
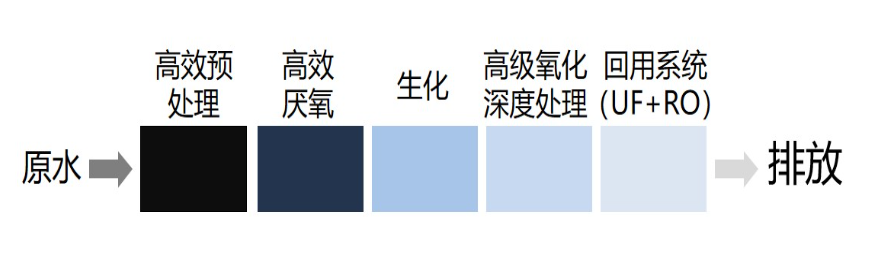
全方位工艺优势彰显:
投资成本优化:由于在废水进入回用系统前,COD 已降至 100mg/L 以下,氨氮<15mg/L,因此采用常规抗污染卷式膜即可满足生产要求,无需依赖昂贵的特殊膜组件。这使得吨水投资大幅降低至 2 - 3 万元,相比传统工艺,投资成本显著减少,为垃圾发电厂在处理渗滤液方面节省了大量资金,提高了项目的经济可行性。
设备寿命延长与稳定性提升:创新工艺有效减轻了膜污染,使得污水处理设备的使用寿命得以延长至 10 年以上,膜寿命也可达到 5 年以上。这不仅减少了设备更换频率和维护成本,还提高了整个处理系统的运行稳定性和可靠性,确保了垃圾发电厂能够长期、持续地对堆酵渗滤液进行有效处理,减少因设备故障导致的停机时间和处理效率波动。
运行成本降低与效益提升:在运行成本方面,该工艺展现出了显著优势。由于采用了高效预处理和高级氧化深度处理,碱及清洗剂用量大幅度减少,吨水处理成本能够有效控制在 40 - 60 元 / 吨水之间。这相较于传统工艺,运行成本大幅降低,提高了垃圾发电厂的运营效益,使其在处理渗滤液的同时,不会因过高的运行成本而陷入经济困境。
废水回用率攀升与资源利用最大化:得益于进膜水质的显著改善,膜产水率得以提高,从而实现了废水回用率的大幅提升。这意味着更多的处理后废水能够回用于发电厂冷却循环水补水,最大限度地实现了水资源的循环利用,减少了对新鲜水资源的取用,在水资源日益紧张的当下,具有重要的战略意义和环境价值。
膜浓缩液品质改善与综合利用便利:经过高级氧化处理后,膜浓缩液的水质得到极大改善,出水无色、无味。这使得膜浓缩液能够直接用于石灰制浆,不仅操作环境得到优化,减少了异味和污染排放,还提高了石灰制浆的质量和效率,实现了膜浓缩液的有效综合利用,避免了传统工艺中浓液处理的难题,进一步提升了整个处理工艺的环保性和资源利用率
本文出自广州市勃发环境科技有限公司,转载请注明出处!更多垃圾发电厂垃圾堆酵渗滤液处理技术资讯请访问www.gzbofa.net
24小时热线电话:13822165057